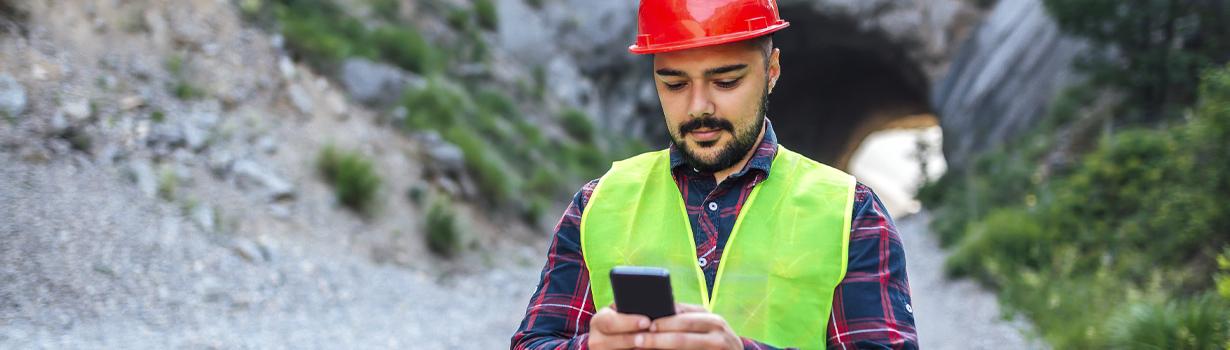
REMEDIATING RIVERVIEW MINING SUBSIDENCE WITH PARALINK GEOGRID
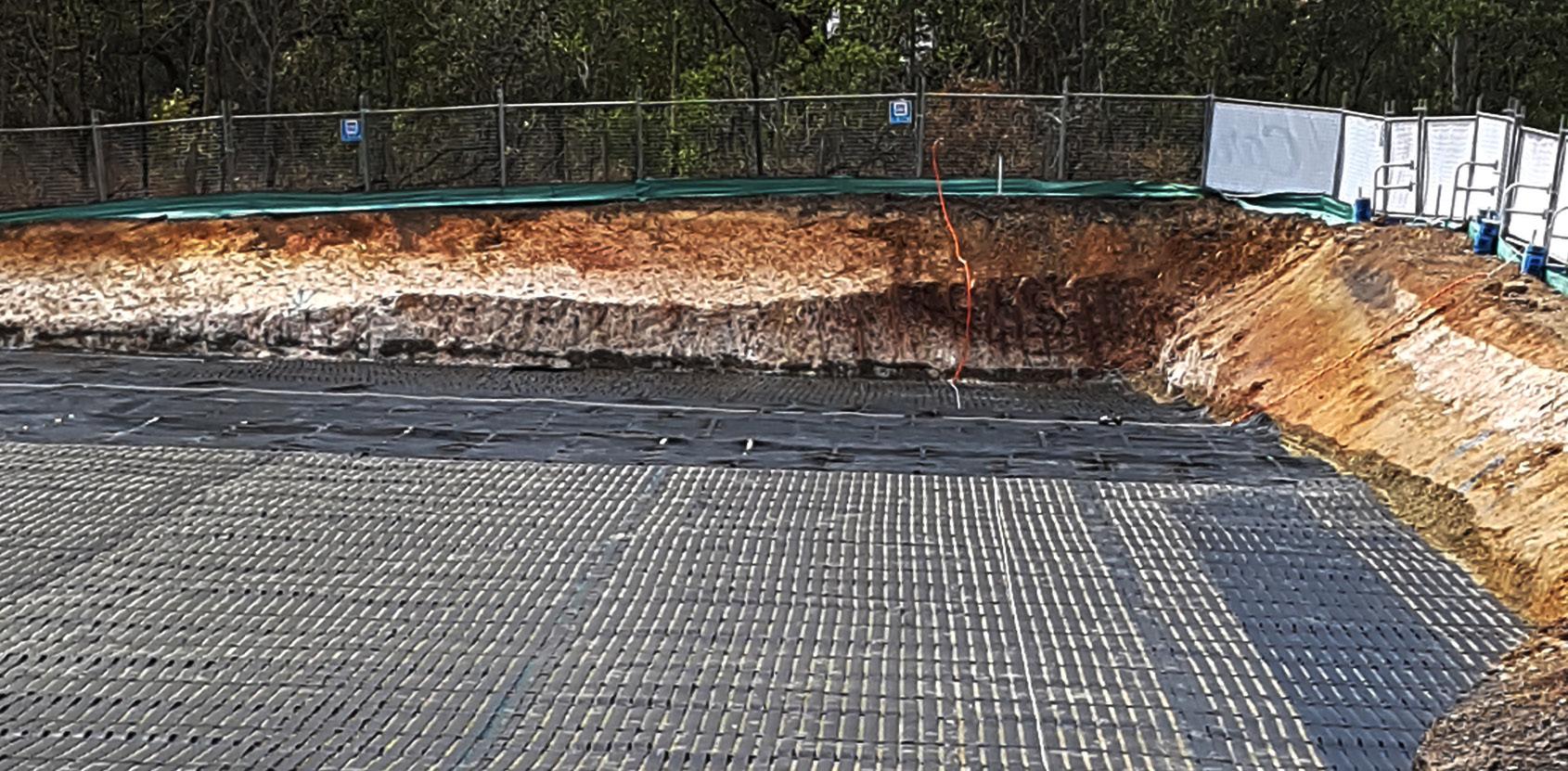
A service station was proposed to be built in Westphalen Drive, Riverview. A previous mine subsidence report identified the presence of historical mining activity beneath the site and the potential for sinkholes to occur.
Due to recent rapid urban growth in Queensland and to meet the land demand, development in subsidence prone areas is an attractive option for developers due to the lands relatively low cost. From previous work conducted at the site, it was concluded that from the results of the sonar, the sizes of the workings appear reasonably consistent with the mine workings plans and that designing for a 6m diameter void over a single bord or a 10m diameter void over a bord intersection appeared to be a reasonable approach.
This previous work assessed the location and nature of the bord and pillar workings, and that the significant subsidence risks comprised sinkhole development due to collapse of bords. The building foundations were designed by the structural engineer as structural rafts to span the potential sinkholes. Other key features that are settlement sensitive (i.e. fuel storage tanks) have been located over stable areas of the site directly underlain by coal pillars Commonly used remediation measures for subsidence caused by voids are wide-scale grouting of the underground cavities, providing structural bridging using a reinforced concrete slab or raft and deep foundations (piles or piled raft). These remediation methods are not economically viable for low rise buildings or infrastructure developments.
Commonly used remediation measures for subsidence caused by voids are wide-scale grouting of the underground cavities, providing structural bridging using a reinforced concrete slab or raft and deep foundations (piles or piled raft). These remediation methods are not economically viable for low rise buildings or infrastructure developments.
Flexible bridging platforms consisting of high strength geosynthetic reinforcement are a cost-effective, viable option. The premise of this approach is not to prevent any surface deformation occurring but to maintain the serviceability of the surface until remediation measures can be undertaken. Douglas Partners conducted the analysis and design of a geogrid reinforced fill bridging platform to accommodate the anticipated sinkhole subsidence. The analysis was carried out using finite element software Plaxis 2D (Version 2017) and was based on the British Standard BS 8006-1:2010.
Maximum differential surface deformation (ds / Ds) should be limited to 1% for principal roads (applicable speed of 90km/h) and 2% for non-principle roads (applicable speed of 60km/h). ds is the surface deformation, and Ds is the diameter of subsidence or diameter of the sinkhole (Fig 74 from BS8006.) Within the service centre, the maximum speed limit can be restricted to 20km/h, and the assessment of the level of acceptable risk against construction costs and potential remediation costs resulted in modified design criteria being adopted. It is noted within the British Standard that higher levels of ground settlement may be tolerable if voids forming during the life of the structure are to be backfilled (as preferred by the developer for this project). A maximum allowable differential surface deformation of 5% (300mm) was considered based on the 20km/h speed restriction, and if a sinkhole occurs, large surface deflections will be tolerable for limited periods (and it is likely that the area would be cordoned off and not remain open to traffic) prior to backfilling (i.e. grouting) of voids.
A double-layer system design was selected, one that utilised Maccaferri’s high-performance ParaLink geogrid 1000 kN geogrid in longitudinal and transversal layers. Custom roll sizes were manufactured to minimise wastage and assist with placement. Maccaferri ParaLink geogrids are unique planar structures consisting of a monoaxial array of composite geosynthetics strips. Every single longitudinal strip has a core of high tenacity polyester yarns tendons encased in a polyethylene sheath; the single strips are connected by non-resisting cross laid polyethylene strip that gives a grid-like shape to the composite.
PRODUCT USED
Maccaferri® Paralink® High Strength Geogrid
- Tough and durable polyethylene sheath is resistant to physical, chemical and biological conditions found in basal reinforcement applications and reinforced soil structures, including micro-organisms, UV radiation and mechanical damage
- High modulus and low creep characteristics, sustaining over 64% of their initial strength over a service life of 120 years compared with geogrids made from polypropylene or polyethylene
- Quick and easy installation as they are lightweight, flexible and can be easily cut to the required lengths
- BBA certified for use as basal reinforcement under road embankments constructed on or over soft foundation soils; piled foundations and areas prone to subsidence